構造
「ミュースクラバー」は静止型混合器(Static Mixer)であり、円筒形の塔本体の内部に高性能の気液接触効率を有する撹拌用混合羽根「ミューミキシングエレメント」を内蔵しております。ミューミキシングエレメントは、右捻り及び左捻りの螺旋状の羽根体です。微細粒子及び化学物質を含有する排ガスは、ミュースクラバーの上部から供給されます。
一方、ポンプにより装置下部タンクから供給された洗浄液は、塔本体の側面に配置された散水管に設置したスプレーノズルを介して塔内に噴射します。この洗浄液は、排ガス中の化学物質と粉塵を吸収しつつ、塔の上部から下部へ落下して下流に配置したタンク内に集まり、再び塔内を循環します。すなわち、塔を通過する排ガスと循環する液体は、内設されたミューミキシングエレメント内を並流で通流する間に、分割、合流、せん断及び右、左方向の螺旋状回転を繰り返しながら、気液は完全に混合、接触されます。
一つ目として、この方式による効果は排ガスからの含有物質の捕捉です。前述のように気液接触効率を増大させ、捕捉を高効率で行います。排ガス中の化学物質は化学的に吸収して、又、不活性物質は物理的に溶解して洗浄液に吸収します。又、排ガス中の粉塵の微細粒子は、装置内を通流する間に凝集や膨潤により粒子成長して粗大化します。更に気液の強い混合で塔内に発生する微細な気泡に捕捉されます。従い、微細粒子は洗浄液に容易に捕捉されるようになり、洗浄液に懸濁します。これらにより、排ガスは清浄化されます。
二つ目は、排ガスからの物質の捕捉を装置内の閉塞なしに行なうことです。これは、排ガスと洗浄液の気液混相流とミューミキシングエレメントの相互の連携による効果です。反応生成物及び粉塵等の付着成長による羽根の表面・裏面や空孔の目詰まり、及び装置壁面での成長を防止します。
三つ目は、排ガス処理の通流時の圧力損失の低減です。これは、ミューミキシングエレメントの構造に基づき圧力損失を小さくする効果です。また、塔本体側面に配置する散水管のスプレーノズルからの循環洗浄液の噴き出しによってエジェクター効果を生じさせて、圧力損失の更なる低減化に貢献しています。
この排ガス処理において、ミュースクラバーには適宜新液が供給されます。これは、気液温度制御のためであり、通常は新液の顕熱、蒸発熱を用いた冷却を行ないます。これに加えて、循環液ラインに熱交換器を設置して外部から冷却、又は加熱を行なう方法もあり、そのプロセスに適すように行ないます。新液投入のもうひとつの目的は、タンク内の循環排液中の捕捉物質の濃度制御のためであり、捕捉物質を含有した排出液をタンクの液レベルを維持しつつ排出します。
混合原理
図1に示すように、パイプ内周面に螺旋状の右捻り(右旋回)及び左捻り(左旋回)の羽根体を設置して、複数個の右捻り羽根体及び左捻りの羽根体を、空間部を介して交互に配置しています。羽根体は多数の空孔を有しています。排ガスと洗浄液とは並流で、螺旋状に右に捻った羽根体を通流しながら、分割、合流、水平及び垂直方向のせん断作用により、気液の混合接触が行なわれます。そして、空間部で合流し、次に螺旋状に左に捻った羽根体による再分割、せん断作用により混合接触されます。このように、多分割、旋回、合流、反転作用、及び半径方向と軸方向でのせん断作用を連続的に繰り返しながら気液は完全に混合接触されます。
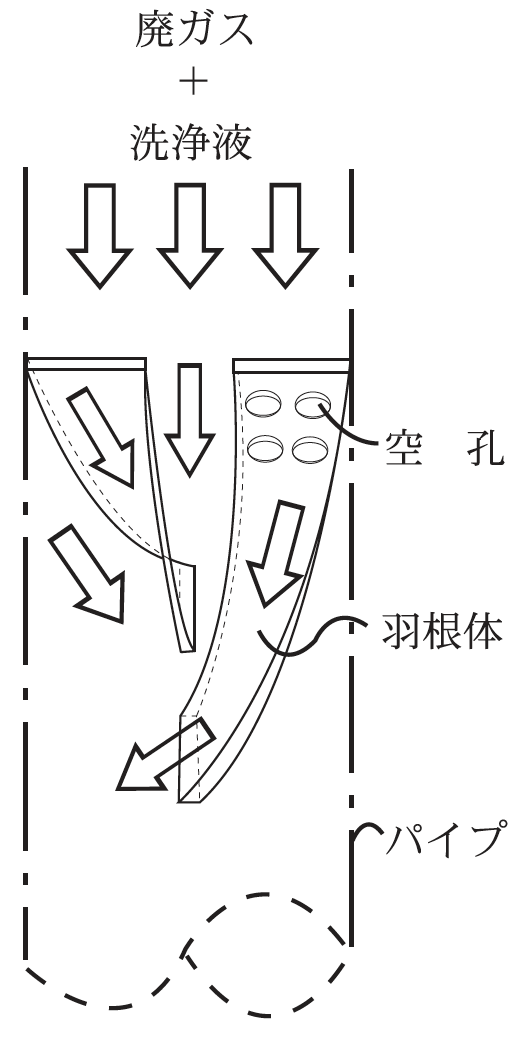
図1.内蔵したミューミキシングエレメントによる気液接触の模式図
混合テスト
ミュースクラバーを使用して、良好な気液の混合、接触状態を得るポイントは、以下の二点です。
- 液/ガス比を高くする(ガス流速が一定下)
- ガス流速を速くする(液/ガス比が一定下)
これを、実験で確認するために、内径72mmの管に小型ミューミキシングエレメントを図2のように配置して、上部から下部方向に水を流すと共に、常温の空気を水と並流で通流するテストを行いました。図3の写真撮影した透明管部分のゾーンは、二つのミューミキンシングエレメント間の空間で空洞です。そこでは、空気と水の混合状態を目視で観察でき、幾つかの条件のテスト結果を示します。まず、空気流速10m/secにおいて水/空気比を70~8ℓ/m3まで変化させました。この時、水/空気比8ℓ/m3まで水が低下すると混合は不良ですが(写真(d))、それよりも水量の多い70~15ℓ/m3(写真 (a)-(c))の範囲は、良好です。
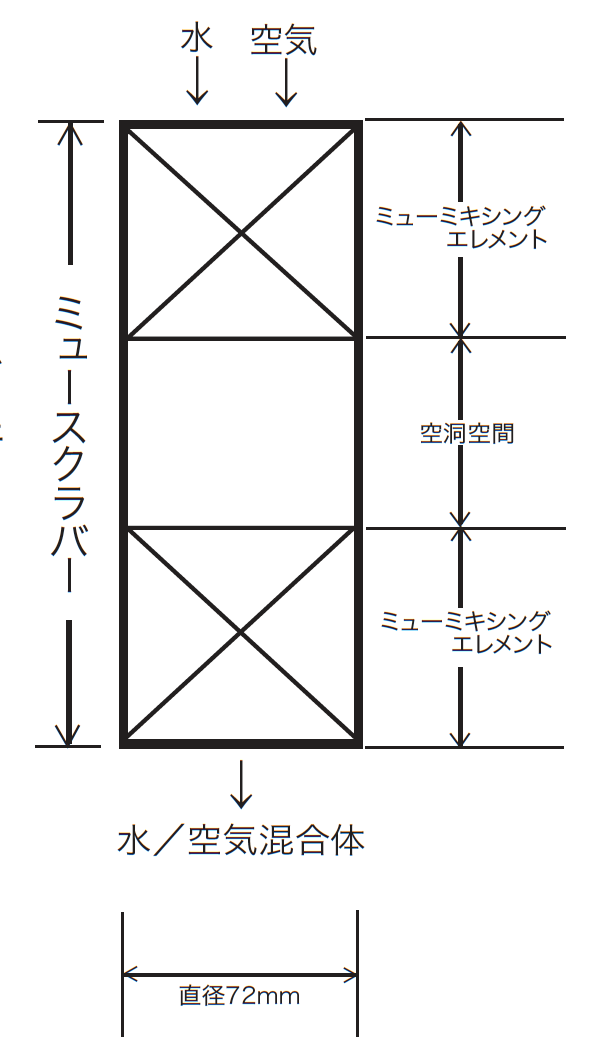
図2.観察に用いたミュースクラバーのセッテイングの模式図(図中に写真撮影部分を表示)
次に空気流速を半分の5m/secにしました。この時、水/空気比15 ℓ/m3の混合状態は、不良でした(写真(e))。これに対して、流速10m/secのケースは、同じ水/空気比15 ℓ/m3であっても、写真©のように混合状態は良好でした。これにより、流速が速いと混合が良くなることが分かります。この時、水/空気比15 ℓ/m3の混合状態は、不良でした(写真(e))。一方、流速が半分の5m/secでも、水/空気比を35ℓ/m3まで高めると、混合状態は再び良くなりました(写真(f))。これらのテスト結果により、液ガス比、ガス流速はそれぞれ増加すれば気液の混合状態は良好になり、その逆の場合は悪化することを観察できました。
気液混合状態の写真
図3. 気液混合状態の写真(※液ガス比= 液量(ℓ/h)/ガス量(m3/h))
8つの特長
01 コンパクトに、排気ライン上に設置できます
ガス空塔速度は2~20m/secであり、排気管の途中に設置できます。気液は並流なのでフラッディング現象が起きず、塔内流速を最大20m/secで運転することができ、コンパクト設計で設備費が低減します。
02 低い圧力損失です
操業時は、塔内をガスが通流するとともに液を循環します。その液ガス比は0.2~500ℓ/m3の範囲ですが、良好な気液接触を得るために、ガスの最小流速2m/sec近傍では液ガス比は50~500ℓ/m3と高目に設定します。又、最大流速の20m/sec下では液ガス比は低目で0.2~20ℓ/Nm3の範囲です。低圧力損失を求める場合は、圧力損失ゼロの運転も塔内流速を低くしたり液ガス比を小さくしたりして可能です。これに反して、気液接触効率を最大限に上昇させる、高流速、且つ高い液ガス比の条件下では、圧力損失は通常運転の3kPaG以下を外れて増加する場合があります。
03 目詰まりがありません。メンテナンスフリーです
付着性の強い粉塵を処理したり、気液接触部で金属酸化物等の固体を析出したりする過酷な要求の気液混合の条件下であっても、生成物による目詰まりを完全に防止して、長時間、連続運転(8,000時間/年以上が通常で、15年間連続運転の実績も有り)ができます。また、長期運転後に装置洗浄を行なう際は、装置の分解と洗浄作業を容易に行なうことができます。
04 粉塵、ミスト、化学物質の捕捉は高性能です
除去効率は、1塔あたり化学物質の吸収で90~99.99%以上です。プロセスの組み方次第で99.999%以上も可能ですが、化学物質の性質にも拠ります。また、1ミクロン以下の粉塵やミストは通常は90%以上の除去効率ですが、洗浄液との相溶性によって変化します。もし、更なる除去効率の上昇が必要な場合は、通常はエレメント数を増やすことで容易に対応することができます。
05 高濃度、及び低濃度ガスの両方の処理に適します
数十容積%以上の高濃度の化学物質を含有する排ガスであっても容易に処理できます。空気や窒素で希釈する必要はありません。また、気液接触効率が高いため、数十容積ppmの低濃度の化学物質の処理にも適します。
06 気液接触効率が高いので、気液平衡の実現を仮定して簡素に設計できます
化学吸収、蒸発凝縮の相変化、又はヘンリー法則に基づく物理吸収などを気液平衡データに基づき、気液の組成、温度、並び必要熱量を求めて設計します。気液中の化学物質の吸収、脱着に関して、ミュースクラバー内で気液平衡へ到達することを幾つかの例で確認しております。洗浄液が水である場合に水の蒸発・凝縮は、気液平衡に到達します。
07 捕捉と冷却を同時に行なう機能があります
排ガスから粉塵及び化学物質を捕捉すると同時に、気液の冷却を行ないます。この同時機能を備えていることはミュースクラバーの利点です。
08 並流式ばかりでなくて、目的に応じて向流式を使います
限られた特殊なケースでは、向流設計を行います。このケースは、多段のミューミキシングエレメントに蒸留塔のような考えを適用し理論段数を求めます。この時、もし吸収速度の遅い物質ならば段数にゆとりをもちます。吸収においては、排液中の化学物質濃度を高め、且つ、排ガス中の化学物質濃度を極微量に低下します。一方、放散に使うと吸収液から高濃度の化学物質を気体として回収して、且つ、放散後に残った吸収液の化学物質濃度を極力低下させます。また、並流と向流の組み合わせを、最適設計として用いる場合もあります。
用途及び設置例
ミュースクラバーには、排ガスの清浄化、排ガスからの化学物質回収などの使い方があり用途は以下のようです。
- HCl, Cl2, HF, SOX, NH3, NOX, Hg, DXN’s等を含有する排ガスの処理
- 四塩化ケイ素、三塩化ケイ素、二塩化ケイ素、フッ化ケイ素、四塩化チタンなどと水の接触で金属酸化物固体を生成する排ガス処理
- 排ガス中のSiO2, ZnOなどの金属酸化物の除塵
- アンモニア、トリエチルアミン、硫化水素等の微量の悪臭成分の吸収による脱臭
- 排ガス中の細菌やウイルス等の生物のオゾンガス等による滅菌、殺菌
- 排ガスからのNH3, HClなどの化学物質の回収
- 薬品原体の除塵と回収
次章に5つの設置例を示します。
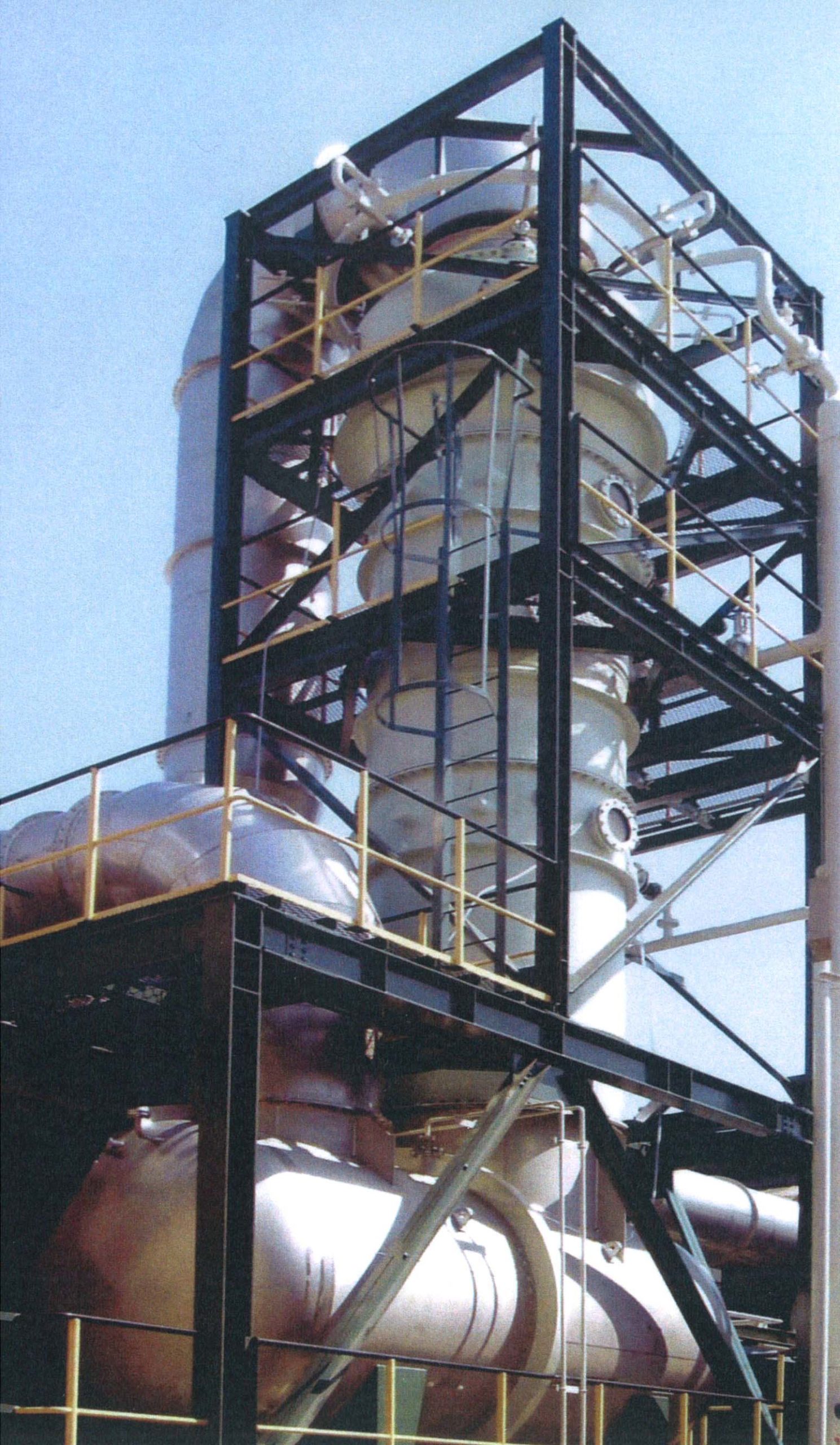
【排ガス除塵塔】寸法 φ1800×8mH
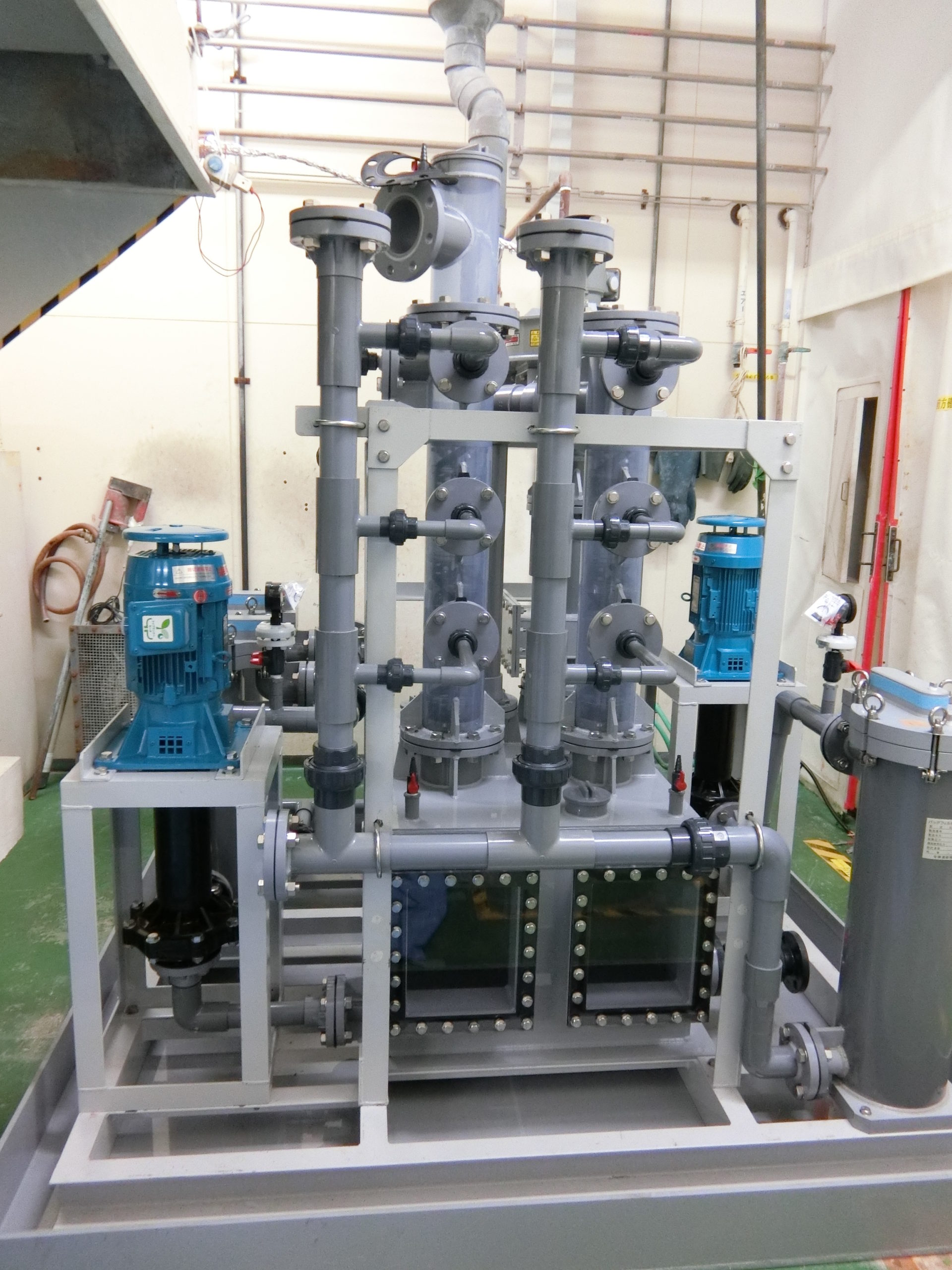
【CVD排ガス処理装置】CIMG2669
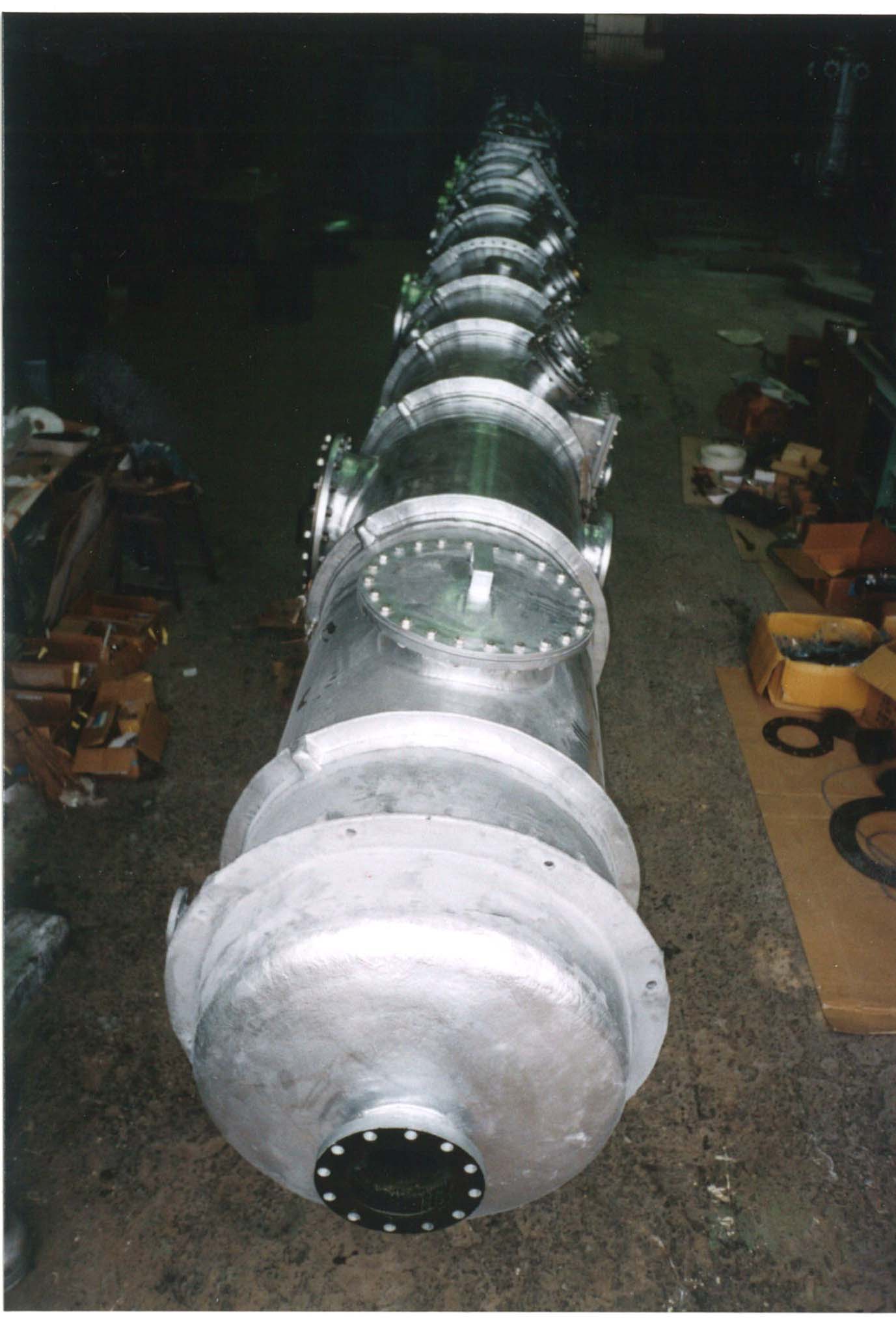
【HClガス吸収塔】寸法 900A×20mH
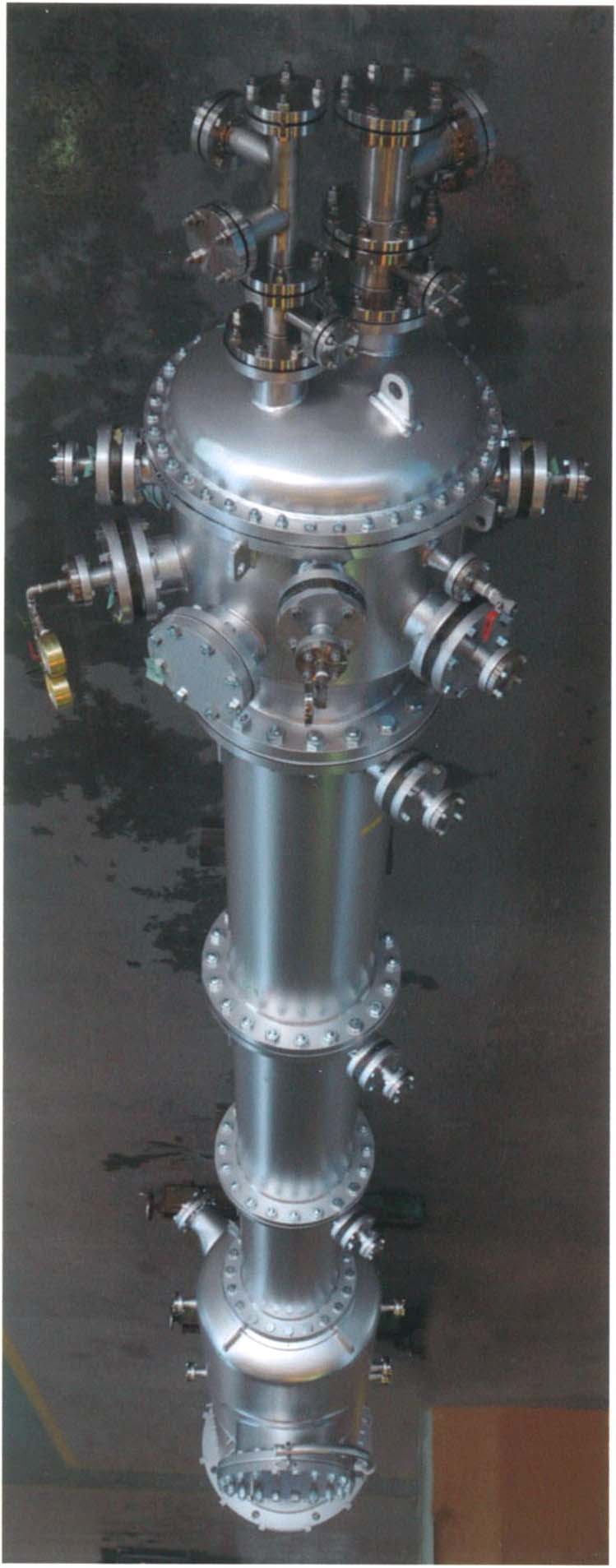
【TiCl4の吸収塔】寸法 500A×9mH
ミュースクラバー設置例
ご照会について
ミュースクラバーのご照会時には、以下に示す設計条件の開示が必要です。ミュースクラバー適応の適否を判断した上で、プロセス、及び装置仕様の検討を行なうためです。なお、以下はほぼフルの設計条件を示します。必要な検討精度に応じてご開示をいただければと考えています。
-
-
- 処理風量: ( )Nm³/h
- ガス温度:運転( )℃、設計( )℃
- ガス元圧力:運転( )kPaG、設計( )kPaG
- 装置入口圧力:運転( )kPaG、設計( )kPaG
- 排ガス含有成分と気体、液体、固体の区別:含有成分a., b., c………について
- 排ガス含有成分の濃度:含有成分a., b., c………を、容積%、容積ppm、mg/Nm³など、明確な単位で表す。
- 処理後の含有成分濃度:含有成分a., b., c………を、容積ppm、mg/Nm³など、明確な単位で表す。
- 許容最大圧力損失:運転( )kPa、設計( )kPa
- 設置場所:屋外、屋内の区別
- 設置面積:幅、奥行、高さ
- 防爆対策:要否の区別
- 電源:電圧等
- 材質:製作者一任、または指定指定の場合は、
材質PVC, FRP, SUS, チタン、他を下記各部位で指定ください。塔本体、ミキシングエレメント、循環液槽、液配管、ガス配管、循環液ポンプ、排風機、フランジ、ガスケット、ボルト・ナット、架台・共通ベース
- 予備品:ミキシングエレメント、スプレーノズル、ガスケット、ボルト・ナット
- 運転状況:運転時間 hr/day、バッチ・連続の区別
- 投入新液:物質名、温度、圧力、溶解物質濃度、PH、比重、粘度
- 排出液:物質名、温度、溶解物質濃度
- 既存情報の活用:現有設備のフローシート、現有設備の問題点、テストデータの開示
- ユーティリティ条件:排ガス処理に必要とするユーティリティ情報の開示
-
各種比較
各種スクラバーとミュースクラバーとの性能比較